Dock Lifts are a safe, effective way to transfer materials and goods between trucks and docks. They reduce the risk of injuries and the handling costs associated with vertical transfer solutions.
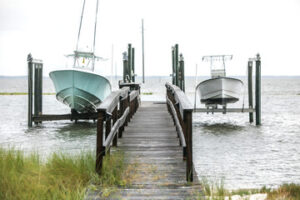
There are several types of dock lifts including portable, top-of-ground and pit mounted lifts. Each is designed for a different load.
One dock-related injury costs an average of $1 million to a company in workers’ compensation, product and equipment damage, loss of productivity, higher insurance premiums and liability. Accidents in the dock area are frequent and can be devastating. They often include injuries caused by trailer creep, unscheduled truck departures, lift-truck tip over and falling loads.
Using dock lifts eliminates these risks, and also provides the safety features required for safe loading operations. They are the only equipment capable of moving freight directly from truck bed height to ground level without manual handling or movement on the forklift. They provide a much safer transition for load transfer than either ramps or skate conveyors.
Dock lifts are available in a variety of sizes and capacities to accommodate most truck sizes. They can even be built into a wall, saving you the cost of a pit. In addition to standard models that mount on cradles, there are semi-portable units that can be mounted on concrete ramp pads for use where a pit is not possible.
When selecting a dock lift, be sure to consider the axle ratings of the vehicles you plan on using it with. Powered pallet jacks and straddle stackers usually concentrate 60% of their payload plus equipment weight on one axle, while sit-down rider fork trucks can have up to a 90% concentration. Compare these axle ratings to the dock lift’s end-load capacity.
Some lifts are rated for slow-speed drive over capability in case a vehicle is unable to stop in time and drives over the lift at the end of its travel range. While this is an excellent safety feature, you should still carefully evaluate a lift’s axle rating capacity if your operation includes large specialty vehicles or if you expect frequent drive-overs of the lift at speeds above its minimum rated speed.
Durability
A good Dock Lift is like a five-star hotel for your PWC – keeping it safe and clean from the harsh elements. It is also like a personal trainer, keeping your watercraft fit and ready to hit the waves at a moment’s notice. Dock lifts generally don’t have many moving parts or a great deal of complexity, making them easy to maintain and care for.
Dock lifts are built to withstand a variety of conditions and uses. They are designed to be strong enough to handle the load capacity of your boat and to resist corrosion from chemicals and saltwater. They also need to be able to handle the vibrations and stress of frequent lifting and lowering of your boat, as well as the force of the wind on the sleeve.
Loading dock lifts, also called dock levelers, bridge the gap and height difference between a loading dock and truck or trailer during loading and unloading operations. They enhance productivity and improve safety, reducing labor costs and product damage. These versatile tools are used in a variety of industries and applications, including warehouses and distribution centers.
Some specialized dock lifts are designed to support sit-down rider fork trucks, providing greater versatility in the warehouse or distribution center. They can be top-of-ground or recessed and have ramps on both ends, with additional truck bumpers to handle impact on one end.
Depending on the model, these units may be remotely powered with a fan cooled hydraulic power unit, valve manifold, relief and solenoid, filter and oil filled reservoir. They are often constructed of stainless steel and aluminum, which offer superior corrosion resistance. They are equipped with beveled toe and fall protection velocity fuses and have a hinged bridge and handrails.
Portability
Some facilities are not equipped to install a permanent dock lift. These sites benefit from the added flexibility of portable lifts or top-of-ground lifts that can be easily relocated if business operations change. These units are often less expensive than pit-mounted dock lifts because they do not require the cost of a concrete pit and ramp construction.
Using a Dock Lift can save time and money when compared to traditional methods for moving goods between truck beds and warehouse floors. Manually unstacking pallets or transferring materials to and from trailers requires a lot of bending, twisting and lifting. This labor intensive process often results in back, shoulder and hand injuries for workers. By using a dock lift, operators remain standing on a level surface and are able to move materials more quickly with less risk of injury.
Dock lifts are available in a wide range of capacities from 4,000 lbs up to 15,000 lbs. Platform sizes are also available to match various application requirements. Each model can be built to accommodate specific handling equipment including carts, pallet jacks, straddle stackers and sit-down rider fork trucks. The maximum lift capacity is determined by adding the weight of the load being transferred plus the lifting capability of the transporting equipment.
Portable, medium-capacity PDQ dock scissor lifts have a low 4 1/2” profile and three open platform sides that make them well-suited for pass-through dock applications of pallet jacks or cart transfer for laundry, postal or retail service. They are typically powered by either an onboard hydraulic power unit or a remote power unit. Many models are designed with safety chains at both ends of the platform and have a detachable hand rail for added operator safety.
Controls
Dock lifts have a limited number of moving parts and are fairly easy to maintain. They can be equipped with a variety of controls to suit the particular application and the environment in which it will operate. Common features include tilting and rotating functions for load transport, wheels to facilitate movement and stabilizing outriggers for dock mounting. Some models come standard with hand or safety rails for personnel protection.
There are many different mechanisms by which a dock lift (dock leveler) can achieve lifting action including scissor, screw, rack and pinion and articulated designs. All of these methods allow for vertical lift travel from fully lowered to fully raised position. Other important specifications to consider include the dock lift’s lifting capacity, platform width and length as well as the actuation method.
A typical loading dock lift will have a checkered plate deck that is constructed from heavy-gauge steel supported by a structural substructure. The dock lift’s lip is mechanically locked into place by night locks on each of the four platform corners and swivels 360 degrees to permit easy transition from a lowered position up against the truck bumper to a raised, ready for loading, position.
The lip can be extended a substantial distance from the dock face to accommodate varying dock and truck bed height differences, bumper projections and setback internal truck beds such as with refrigerated trucks. The dock leveler lift motor runs while the lip is extending or retracting to achieve this operation and when the load clears the night lock, it is locked into place automatically with a limit switch signaling the lift’s return to a parked, vertical position.
Unlike traditional dock levelers that are installed on the side of the warehouse and use a short ramp, the dock lift mounts within the dock face for complete dock-to-ground access and can accommodate all vehicle sizes. They also offer the added benefit of a bi-parting gate to facilitate trailer pickup without having to leave the dock position.
Power
Dock lifts don’t require a lot of moving parts and have few controls, making them easy to maintain. Most lifts simply have a ramp on rollers that you pull your PWC onto with a flick of the throttle. Some even have a built-in winch, which can help you haul your watercraft back up the ramp for transport or storage. This makes them an excellent option for those who don’t want to deal with the added hassle or cost of a trailer.
You can choose the right capacity dock lift by calculating the maximum weight of goods and handling equipment that will be loaded and moved across the platform. Once you know the average load size and a rough estimate of the number of loads that will be handled each day, this can help you decide on a platform size and capacity.
Pit-mounted dock lifts have standard capacities from 5,000 to 15,000 lbs. Portable dock lifts have capacities up to 20,000 lbs. These large hydraulic scissor lifts are used as replacements when no dock is available or as a bridge for off loading trucks when a full dock is.
When choosing a dock lift, it is also important to consider the truck axle rating that will travel over the lift in its fully lowered position. The manufacturer can provide this information and you should always consult this limit to ensure the lift will be rated for the largest trucks and specialty vehicles that may be driven over it.
The power unit on a dock lift is a high-pressure gear pump with check, relief, solenoid, and pressure compensated flow control valves. They are mounted inside a NEMA 4 and/or NEMA 12 enclosure to keep dust and moisture out and fuses protected. The standard unit is configured for 240/480 volt single or three phase operation.